- Home
- Applications
- Liquified Natural Gas
LNG - Liquified Natural Gas
Until recently, the Liquefied Natural Gas (LNG) market was a relatively small part of the gas processing world. The market has experienced a transformation fueled by the discovery of vast reserves in North America, Asia’s robust economic growth, larger populations, and the demand for cleaner energy. Together, these phenomenas are having a tremendous impact on the increasingly complex global LNG market.
LNG plants receive natural gas, remove impurities and cryogenically liquefy it. Liquefying is an efficient way to transport natural gas from remote locations and from locations separated by great distances. Purity requirements are very important to the cryogenic process of the LNG plant.
Generally, the gas needs to be sweetened, which typically occurs by means of an amine absorber to remove acid gas components. The sweet gas is then dehydrated, typically by use of a molecular sieve dehydration system prior to entry into the cryogenic process. Operating instabilities in either the sweetening or dehydration sections can easily lead to lost production and substantial operating and environmental costs.
The most effective method to prevent these instabilities is by use of high efficiency filtration systems. As a result, these filtration systems become a key component to the operation of any LNG facility. Pentair Technologies impact LNG processes by:
- Purification of Inlet Gas prior to the Amine System – Prevents fouling, foaming, downtime and degradation
- Optimization of Amine systems – Reduce fouling of columns and absorbers, reduce foaming, degradation, reduce amine make up costs and reduce corrosion and erosion related wear
- Optimization of Molecular Sieve Systems – Prevent contaminant carryover in dehydrated gas
- Protection of Heat Exchangers – Prevent fouling by eliminating their root cause
- Improved Rotating Equipment Uptime – Prevent damage to rotating equipment that causes excessive maintenance and overhauls
- Optimization of Sour Water System - Prevent fouling and downtime
- Particle-Liquid Separations - RO/Boiler Feed Water Quality, Heat Exchanger Protection, Water Wash Discharge, and Slag/Water Purification, Gas and Steam Turbine protection
The abundance of North American natural gas has already begun to reshape the global energy equation. Technological advancements such as hydraulic fracturing and horizontal drilling that allow access to shale gas have been true game-changers. Available supplies in the United States exceed projected domestic demand. “The American Gas Association maintains that the supply and price of natural gas will be stable beyond the near term,” and all indications are the United States will become a LNG exporter by 2016 (note: there have yet to be any exports of LNG produced from North American natural gas outside of Alaska). There are several new LNG projects in the design stage at this time. Lake Charles and Cove Point are two of the busiest areas for the development of LNG facilities.
In summary, the LNG market is expected to play a vital role in the world energy market which has entered a very transformative period. The expected excess gas supply in North America along with the increasing demand in the Asian market indicates rapid growth in the demand for LNG resulting in the need for efficient and effective LNG process and systems. Pentair is already having a tremendous impact on the efficiency of existing LNG systems.
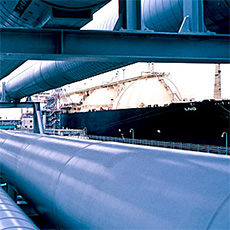
Related technologies
UltiSep technology was developed to address the inherent deficiencies of the conventional gas-liquid separators, making it possible to effectively remove liquid aerosols from gas streams. UltiSep
LiquiSep technology has been implemented specifically to help separate emulsions that are not separable by conventional coalescers. Conventional coalescers are unable to provide the degree clarity associated with LiquiSep technology due to the inability to capture and remove the most penetrating droplets that cause carry-over. LiquiSep can separate these dispersed and emulsified droplets from the hydrocarbon to practically non-detectable levels.
Compared to conventional cartridge filters, COMPAX saves you money by lowering operating costs and reducing disposal costs. When comparing filters with the same efficiencies or Beta ratings, nothing outperforms the cost/performance value achieved with COMPAX.
The Apex element is specifically intended to keep annular velocities constant across the entire height of the element. This is accomplished by introducing a gentle taper in the element, so that the annular space on the outside of the element gradually increased from the bottom to top, keeping pace with the external fluid flow as it exited the element.
The ProcessOR is a superior separator vessel often used for particle/liquid filtration or separation. It is available to be delivered as a self-contained skid (pictured) or a stand-alone vessel. It is also available custom sized as a capital sale or as a turn-key rental, which is often available within days of the received order.
HYDROCARBON RECOVERY TECHNOLOGY - HRT
HRT provides petroleum producers, refiners and gas processors dramatically improved solids control and hydrocarbon recovery from process water streams.
Applications for HRT include: Produced Water Management, Oil Removal from Waste Water, and SRU Optimization.
V-MAX is a coreless filter that flows from the inside-to-outside like a bag filter but V-MAX technology can offer the same online life as a bag filter in a vessel that is roughly half the diameter. This is possible since the V-MAX design offers up to ten times the available filtration media in the same element envelope.